Guarantee: 5 several years
Applicable Industries: Strength & Mining, Other
Bodyweight (KG): .3
Showroom Spot: None
Video outgoing-inspection: Offered
Equipment Check Report: Offered
Marketing and advertising Kind: New Item 2571
Warranty of main elements: 5 several years
Main Components: Bearing, Gearbox, Gear
Construction: Gear
Substance: steel, plastic, aluminum, metal, stainless metal
Merchandise Title: metallic spur equipment
Software: operating system
floor remedy: black coating, Motorbike rear sprocket 428H 36T for CD110 phosphorization
Measurement: m=.5 to m=8, Z≥6, 10mm≤ D≤500mm
Processing: CNC Machining
OEM: OEM Companies Offered
Standard or Nonstandard: Nonstandard Equipment Wheel
Colour: Necessity
Item: AL Metal Stainless steel Copper spur metallic gear wheel
Packaging Details: Every single laptop packed with rust-evidence paper and then with a mesh belt packaging. Then they are packed in cartons.Packing in wooden situations when it is essential
Port: XiaMen
Specification
item | Milling Machine CNC Reducer Gearbox Transmission Major Modest Pinion Spur Gears |
Condition | New |
Warranty | 1.5 years |
Shape | Pinion |
Applicable Industries | Manufacturing Plant |
| 1 |
Showroom Area | None |
Video outgoing-inspection | Not Available |
Machinery Take a look at Report | Not Offered |
Marketing Kind | New Merchandise 2571 |
Warranty of core factors | 1 12 months |
Core Parts | Gear |
Place of Origin | China |
| ZheJiang |
Material | 20CrMnTiH |
Processing | Hobbing |
Standard or Nonstandard | Standard |
Tooth Profile | Bevel Equipment |
| 22.5 Diploma |
Product Identify | metal spur gear |
Application | operating system |
Material | aluminum, steel, stainless metal |
surface treatment | black coating, phosphorization |
Size | m=.5 to m=8, Z≥6, Manufacturing unit Immediate Sale Air Compressor Skillfully Designed Industrial Silent Air Compressor Oil-Less Air Compressor 10mm≤ D≤500mm |
Processing | CNC Machining |
OEM | OEM Services Provided |
Standard or Nonstandard | Nonstandard Gear Wheel |
Color | Requirement |
Item | AL Metal Stainless metal Copper spur metal gear wheel |
Related Merchandise Merchandise Classes Company Profile Manufacturing unit Show Payment & Shipping FAQ
Q : Can I get a sample? A: Of course, we can provide totally free samples for stock things. You just require to spend transport cost If it is a custom made product, there may possibly be CZPT charge occured. Q : How long for generation? A: We have numerous dimensions of inventory, we can ship out in 3-ten times for inventory things. Q : What is your payment time period? A: Payment phrase is usually thirty% TT in progress, Tailored Higher Aspect Hole Precision Stainless Steel Spline Shaft 70% by duplicate B/L. Q : Do you have QC ? A: Of course, we have QC crew who will inspect uncooked substance, each and every procedure in the course of production, goods measurement and mechanical residence, testing result will be loaded in laptop Q : Is the test report traceable? A: Yes, examination report for every batch is loaded in laptop with thorough report, we can get it out at any time. Q : Are you maker or Trader? Reducer Gearbox Transmission Udl Motor Speed Variator Equipment Pushed Jacks1 fifty Ratio Speed Reducer Gearbox A: We are a company. Home
What Are the Advantages of a Splined Shaft?
If you are looking for the right splined shaft for your machine, you should know a few important things. First, what type of material should be used? Stainless steel is usually the most appropriate choice, because of its ability to offer low noise and fatigue failure. Secondly, it can be machined using a slotting or shaping machine. Lastly, it will ensure smooth motion. So, what are the advantages of a splined shaft?
Stainless steel is the best material for splined shafts
When choosing a splined shaft, you should consider its hardness, quality, and finish. Stainless steel has superior corrosion and wear resistance. Carbon steel is another good material for splined shafts. Carbon steel has a shallow carbon content (about 1.7%), which makes it more malleable and helps ensure smooth motion. But if you’re not willing to spend the money on stainless steel, consider other options.
There are two main types of splines: parallel splines and crowned splines. Involute splines have parallel grooves and allow linear and rotary motion. Helical splines have involute teeth and are oriented at an angle. This type allows for many teeth on the shaft and minimizes the stress concentration in the stationary joint.
Large evenly spaced splines are widely used in hydraulic systems, drivetrains, and machine tools. They are typically made from carbon steel (CR10) and stainless steel (AISI 304). This material is durable and meets the requirements of ISO 14-B, formerly DIN 5463-B. Splined shafts are typically made of stainless steel or C45 steel, though there are many other materials available.
Stainless steel is the best material for a splined shaft. This metal is also incredibly affordable. In most cases, stainless steel is the best choice for these shafts because it offers the best corrosion resistance. There are many different types of splined shafts, and each one is suited for a particular application. There are also many different types of stainless steel, so choose stainless steel if you want the best quality.
For those looking for high-quality splined shafts, CZPT Spline Shafts offer many benefits. They can reduce costs, improve positional accuracy, and reduce friction. With the CZPT TFE coating, splined shafts can reduce energy and heat buildup, and extend the life of your products. And, they’re easy to install – all you need to do is install them.
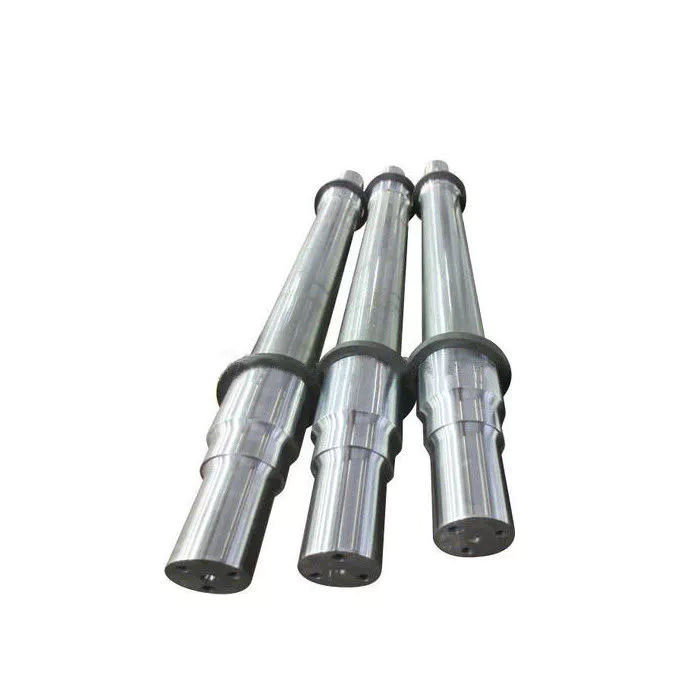
They provide low noise, low wear and fatigue failure
The splines in a splined shaft are composed of two main parts: the spline root fillet and the spline relief. The spline root fillet is the most critical part, because fatigue failure starts there and propagates to the relief. The spline relief is more susceptible to fatigue failure because of its involute tooth shape, which offers a lower stress to the shaft and has a smaller area of contact.
The fatigue life of splined shafts is determined by measuring the S-N curve. This is also known as the Wohler curve, and it is the relationship between stress amplitude and number of cycles. It depends on the material, geometry and way of loading. It can be obtained from a physical test on a uniform material specimen under a constant amplitude load. Approximations for low-alloy steel parts can be made using a lower-alloy steel material.
Splined shafts provide low noise, minimal wear and fatigue failure. However, some mechanical transmission elements need to be removed from the shaft during assembly and manufacturing processes. The shafts must still be capable of relative axial movement for functional purposes. As such, good spline joints are essential to high-quality torque transmission, minimal backlash, and low noise. The major failure modes of spline shafts include fretting corrosion, tooth breakage, and fatigue failure.
The outer disc carrier spline is susceptible to tensile stress and fatigue failure. High customer demands for low noise and low wear and fatigue failure makes splined shafts an excellent choice. A fractured spline gear coupling was received for analysis. It was installed near the top of a filter shaft and inserted into the gearbox motor. The service history was unknown. The fractured spline gear coupling had longitudinally cracked and arrested at the termination of the spline gear teeth. The spline gear teeth also exhibited wear and deformation.
A new spline coupling method detects fault propagation in hollow cylindrical splined shafts. A spline coupling is fabricated using an AE method with the spline section unrolled into a metal plate of the same thickness as the cylinder wall. In addition, the spline coupling is misaligned, which puts significant concentration on the spline teeth. This further accelerates the rate of fretting fatigue and wear.
A spline joint should be lubricated after 25 hours of operation. Frequent lubrication can increase maintenance costs and cause downtime. Moreover, the lubricant may retain abrasive particles at the interfaces. In some cases, lubricants can even cause misalignment, leading to premature failure. So, the lubrication of a spline coupling is vital in ensuring proper functioning of the shaft.
The design of a spline coupling can be optimized to enhance its wear resistance and reliability. Surface treatments, loads, and rotation affect the friction properties of a spline coupling. In addition, a finite element method was developed to predict wear of a floating spline coupling. This method is feasible and provides a reliable basis for predicting the wear and fatigue life of a spline coupling.
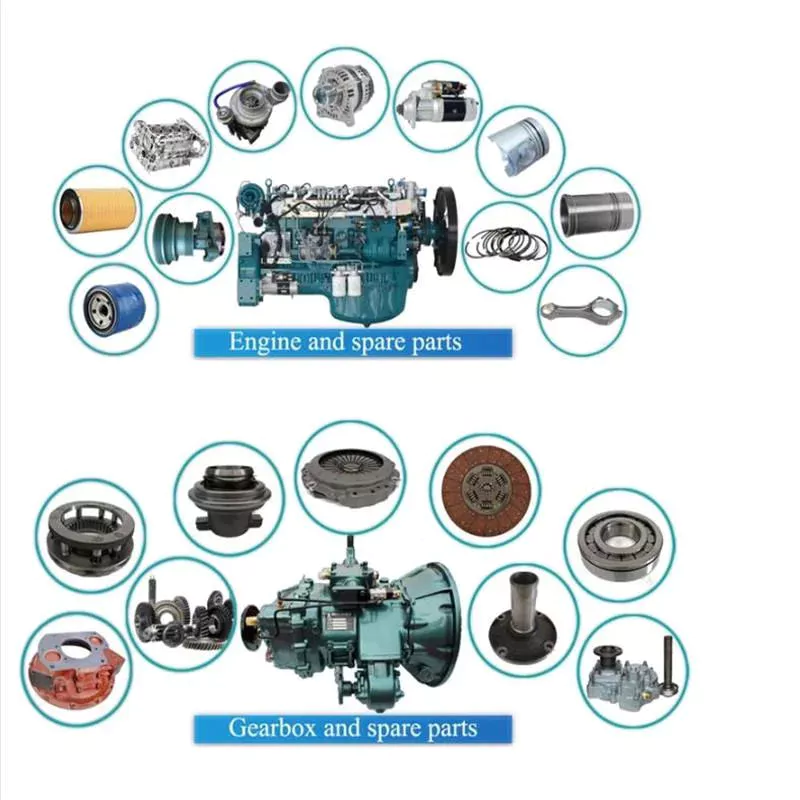
They can be machined using a slotting or shaping machine
Machines can be used to shape splined shafts in a variety of industries. They are useful in many applications, including gearboxes, braking systems, and axles. A slotted shaft can be manipulated in several ways, including hobbling, broaching, and slotting. In addition to shaping, splines are also useful in reducing bar diameter.
When using a slotting or shaping machine, the workpiece is held against a pedestal that has a uniform thickness. The machine is equipped with a stand column and limiting column (Figure 1), each positioned perpendicular to the upper surface of the pedestal. The limiting column axis is located on the same line as the stand column. During the slotting or shaping process, the tool is fed in and out until the desired space is achieved.
One process involves cutting splines into a shaft. Straddle milling, spline shaping, and spline cutting are two common processes used to create splined shafts. Straddle milling involves a fixed indexing fixture that holds the shaft steady, while rotating milling cutters cut the groove in the length of the shaft. Several passes are required to ensure uniformity throughout the spline.
Splines are a type of gear. The ridges or teeth on the drive shaft mesh with grooves in the mating piece. A splined shaft allows the transmission of torque to a mate piece while maximizing the power transfer. Splines are used in heavy vehicles, construction, agriculture, and massive earthmoving machinery. Splines are used in virtually every type of rotary motion, from axles to transmission systems. They also offer better fatigue life and reliability.
Slotting or shaping machines can also be used to shape splined shafts. Slotting machines are often used to machine splined shafts, because it is easier to make them with these machines. Using a slotting or shaping machine can result in splined shafts of different sizes. It is important to follow a set of spline standards to ensure your parts are manufactured to the highest standards.
A milling machine is another option for producing splined shafts. A spline shaft can be set up between two centers in an indexing fixture. Two side milling cutters are mounted on an arbor and a spacer and shims are inserted between them. The arbor and cutters are then mounted to a milling machine spindle. To make sure the cutters center themselves over the splined shaft, an adjustment must be made to the spindle of the machine.
The machining process is very different for internal and external splines. External splines can be broached, shaped, milled, or hobbed, while internal splines cannot. These machines use hard alloy, but they are not as good for internal splines. A machine with a slotting mechanism is necessary for these operations.


editor by czh 2023-02-19